Aggregate Supply System
① Modular structure with walkways and ladders.
②The feeding speed of cold aggregate can be adjusted by frequency converter.
③ Belt conveyor with protective device, including emergency stop idler, anti-reverse idler and sidewall belt.
④ Automatic compensation system, aggregate shortage alarm device.
⑤ Each cold aggregate bin is equipped with a screen to filter oversized aggregates.
⑥ The vibrator is installed on the fine aggregate bin.
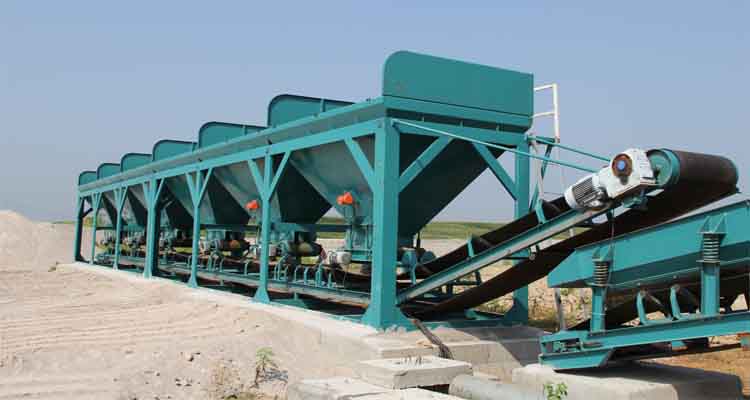
Drying System
①High-efficiency dust removal and filtration system, the drying drum is connected to the bag filter to shorten the dust filtration distance and improve the dust filtration effect.
② The drying drum is made of wear-resistant and temperature-resistant materials, which are sturdy and durable.
③The transmission device is in close contact with the drying drum.
④ The drying cylinder has a thermal insulation layer (50mm thick, rock wool) and a protective cover (stainless steel).
⑤ Transmission device includes motor with inverter, anti-vibration device and lubrication system.
⑥ The temperature sensor is installed on the outlet of the drying drum.
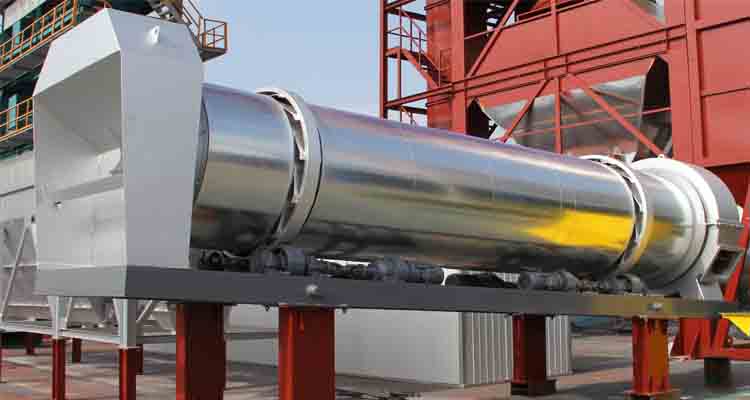
Screening System
① Vibrating screen with optimized structure, high efficiency and low power consumption.
② Each vibrating table consists of two halves, which are easy to replace and maintain.
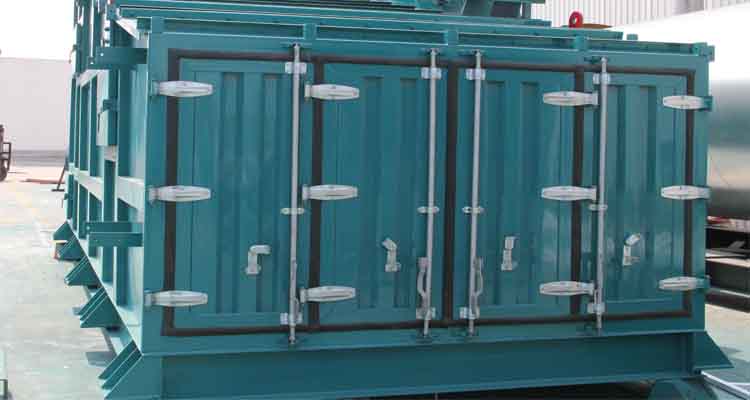
Weighing System
① The hot aggregate silo is equipped with a liquid level indicator.
② Install slag discharge pipe and overflow pipe on the stirring tower.
③ The weighing system includes a weighing sensor (loading sensor), and the signal is directly transmitted to the control computer; the weighing system has an automatic compensation function.
④ Load cell: Germany FLINTEC.
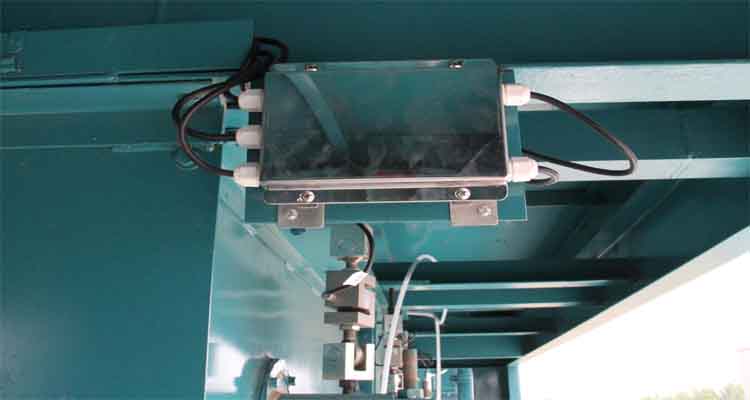
Mixing System
① The stirring arm, paddle and lining plate are all made of wear-resistant materials.
②Double shaft mixer is driven by synchronous motor, 3D mixing inside the mixer, better mixing performance.
③Bearing: Swiss SKF.
④ The walkways and ladders on the mixing tower are made of hot-dip galvanized materials.
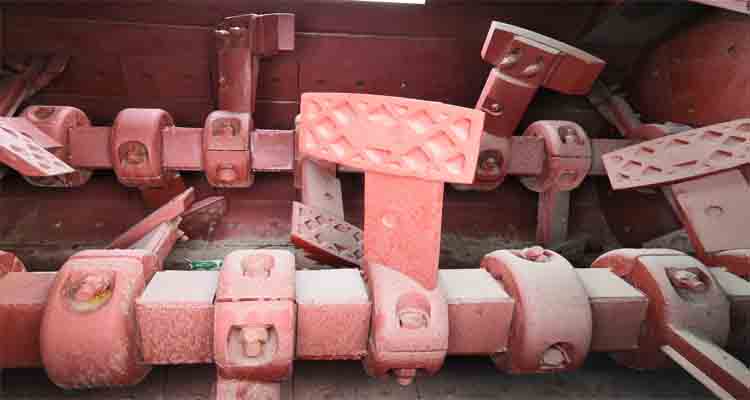
Dust Collection System
①Two-stage dust filtration system: gravity type and bag filter.
② The gravity filter is in front of the bag filter.
③The bag filter adopts NOEMX cloth bag with thermal insulation layer (50mm, rock wool).
④ Pulse jet dust filter.
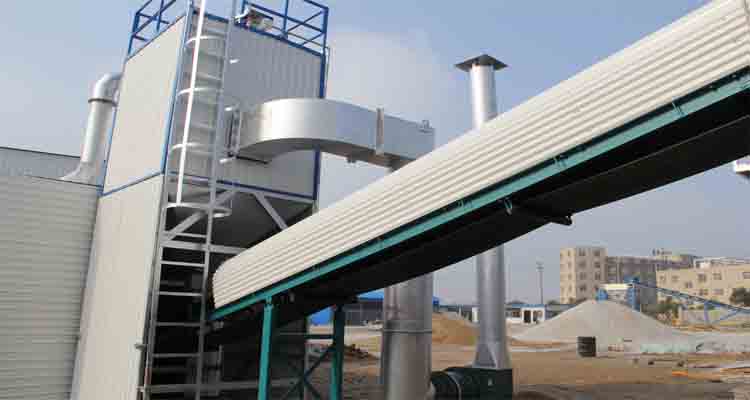